Vantaggi dei compositi innovativi in Aramide AFRP nei progetti Sismabonus
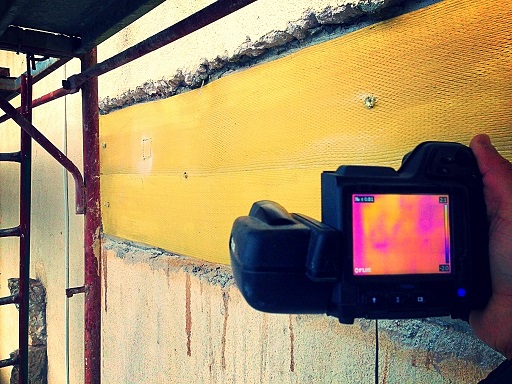
Negli ultimi anni oltre alle tradizionali fibre di vetro e di carbonio utilizzate per il consolidamento strutturale di edifici in c.a. e muratura è cresciuto sempre più l’utilizzo dei compositi in fibra di aramide AFRP grazie alle elevate caratteristiche fisico meccaniche di tale fibra.
La fibra aramidica, infatti, è l’unica fibra caratterizzata da una resistenza propria al taglio e tranciamento che la rende indispensabile in numerose applicazioni di rinforzo oltre ad essere caratterizzata da un’elevata resistenza alle alte temperature.
Numerosi sono gli interventi di consolidamento strutturale realizzati con questi innovativi materiali di consolidamento sia in Italia che in Centro America.
OLY TEX ARAMIDE 400 UNI AX HR è l’unico sistema AFRP, certificato in Italia presso il C.S.LL.PP. con il quale è possibile realizzare interventi di rinforzo strutturale ai sensi del CNR D.T. 200/R1 2013.
Le Fibre aramidiche
Le fibre aramidiche sono fibre polimeriche sulla base di poliammide aromatici. Nei materiali compositi la fibra commercialmente più importante è la fibra ad alto modulo, la quale è stato introdotto nei primi anni ’70 con il nome commerciale Kevlar. Il kevlar possiede una grande resistenza al calore e alla fiamma. Per le sue caratteristiche di resistenza viene utilizzato come fibra di rinforzo per la costruzione di giubbotti antiproiettile, di attrezzature per gli sport estremi e per componenti usati in aeroplani, imbarcazioni e vetture da competizione.
Nel corso degli anni, questo tipo di fibra polimerica ha ricevuto miglioramenti notevoli in termini di resistenza meccanica. Con il tempo si è arrivati a prodotti sempre più resistenti, che offrono un rapporto di almeno 5:1 sull’acciaio ed è molto resistente anche alla temperatura.
Produzione
Il kevlar si ottiene per condensazione in soluzione a partire dai monomeri fenilendiammina (para-fenilendiammina) e cloruro di tereftaloile. Come sottoprodotto di reazione si ottiene acido cloridrico.
La produzione è simile ad altre fibre polimeriche: polimerizzazione, estrusione, stiramento. Il polimero viene sciolto in un liquido ed estruso ad una temperatura di circa 200 °C mentre evapora il solvente. L’estrusione può avvenire soltanto dalla soluzione in quanto il punto di fusione della fibra è molto più alto della temperatura di decomposizione. Il prodotto di questa fase ha soltanto circa il 15% della resistenza e il 2% della rigidità della fibra finale. Il polimero ha una struttura a bastoncini con poco orientamento rispetto all’asse longitudinale della fibra. Si ottiene una cristallizzazione e l’orientamento della struttura stirando la fibra a 300-400 °C.
I principali vantaggi delle fibre aramidiche sono:
- alta tenacità;
- resistenza all’impatto;
- capacità di assorbimento delle vibrazioni;
- buona inerzia chimica ed elettromagnetica;
- basso peso specifico;
- resistenza alle alte temperature;
- resistenza alla fiamma;
- resistenza a taglio;
- elevata resistenza e modulo elastico;
Perché scegliere la fibra di aramide?
L’aramide, anche noto come Kevlar, è un materiale caratterizzato da elevatissime caratteristiche fisico meccaniche.
I sistemi compositi a base di fibra di aramide sono caratterizzati da:
- Elevate caratteristiche di resistenza a trazione e modulo elastico;
- Elevata resistenza al taglio, all’urto, all’abrasione ed all’impatto;
- Resistente al calore ed alla fiamma fino a 200°C;
- Elevata resistenza agli agenti chimici;
La fibra aramidica, grazie alle sue proprietà viene già scelta da:
- La Marina Militare degli Stati Uniti d’America per la realizzazione degli elmetti;
- Il Corpo Nazionale dei Vigili del Fuoco per la realizzazione degli elmetti;
- I corpi armati di tutto il mondo per la realizzazione dei giubbotti antiproiettile;
- Il team da regata «Luna Rossa – America’s Cup» per la realizzazione dello scafo;
- Team Pirelli – Formula Uno, per la realizzazione della struttura dei pneumatici;
- I team di Formula Uno per la realizzazione di alcuni componenti delle auto;
Tra i principali interventi realizzati con questi materiali ricordiamo gli interventi di consolidamento del Real Albergo dei Poveri di Napoli e della Iglesia de Nicoya in Costa Rica.
Palazzo Fuga – Real Albergo dei Poveri